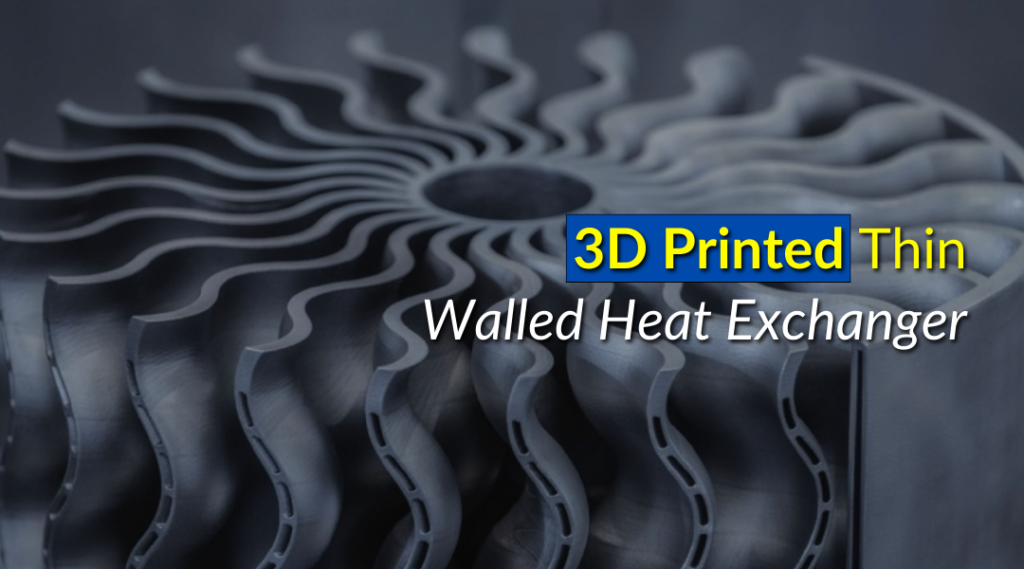
A heat exchanger is a device designed to transfer heat between two different fluids, and it plays a crucial role in various applications such as air conditioners and rocket engines. Traditionally, heat exchangers were manufactured using methods like welding thin sheets of material together, which could be challenging, time-consuming, and result in heavier parts.
The advent of additive manufacturing (AM), particularly with materials like AlSi10Mg, has brought about significant advancements in heat exchanger design and production. AM allows for the creation of intricate and complex geometries that might be impractical or difficult to achieve through traditional methods like CNC machining. This is especially true when designing thin-walled heat exchangers with intricate fins and complex internal structures.
Key advantages of using additive manufacturing for heat exchangers include:
Single-Piece Production: AM enables the creation of heat exchangers as a single, integrated piece, eliminating the need for welding thin sheets together. This results in a more efficient and streamlined manufacturing process.
Smaller and More Efficient Design: Through AM, designers can optimize heat exchanger designs, making them smaller, more lightweight, and more efficient. This is achieved by creating complex minimal surface structures and latticework, improving the surface area-to-volume ratio.
Material Versatility: AM can produce heat exchangers from a wide range of materials, including aluminium alloys and high-temperature alloys like Inconel, copper, and more. This allows for tailoring the material to specific thermal conductivity and mechanical strength requirements.
Customization and Design Freedom: The layer-by-layer additive manufacturing process provides greater design freedom. Engineers can create intricate and customized internal structures, enhancing heat transfer efficiency and overall performance.
Thermal Management Solutions: Additive manufacturing facilitates the design and manufacture of novel and high-performing surfaces integrated into a single component, addressing thermal management challenges effectively.
New Opportunities in Design: Recent developments in additive manufacturing have opened new opportunities for designing complex structures that were previously difficult or impossible to fabricate. This includes exploring intricate geometries, internal structures, and other innovative designs for improved heat exchanger performance.
Reduced Weight and Volume: Objectify Technologies achieved a significant reduction (approximately 30%) in weight and volume compared to equivalent parts produced by conventional methods. This reduction is crucial for applications where weight is a critical factor.
In summary, additive manufacturing has revolutionised the manufacturing of heat exchangers by providing new possibilities in design, reducing weight and volume, enhancing thermal efficiency, and enabling the production of highly intricate and custom components. These advancements contribute to improved overall performance and reliability in various industrial applications.