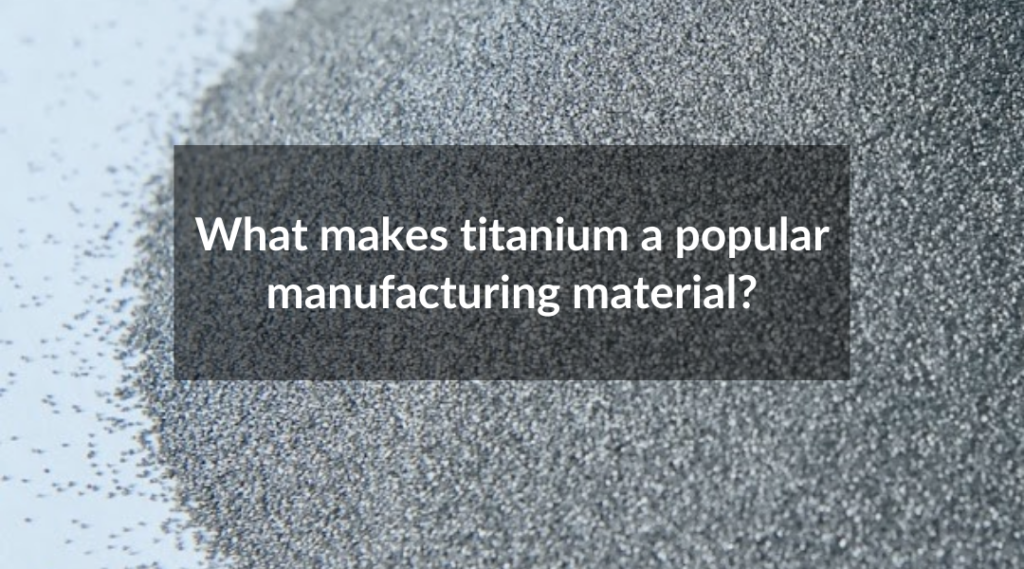
The Allure of Titanium Alloy Powder
1. Lightweight Strength
Titanium alloys are renowned for their exceptional strength-to-weight ratio, making them a preferred choice in aerospace, medical, and automotive industries. The ability to 3D print titanium alloy powder opens new possibilities for designing lightweight yet robust components.
2. Enhanced Customization
3D printing allows for intricate and complex geometries that would be challenging or impossible with traditional manufacturing methods. Titanium alloy powder, when used in additive manufacturing, facilitates the creation of highly customized and optimized parts, meeting specific industry requirements.
3. Corrosion Resistance
Titanium alloys possess excellent corrosion resistance, making them ideal for applications in harsh environments. The 3D printing of titanium alloy powder further enhances this property by enabling the production of seamless, corrosion-resistant components with reduced material waste.

Challenges and Ongoing Research
1. Cost Efficiency
While the benefits of titanium alloys are substantial, the cost of production remains a challenge. Ongoing research focuses on developing more cost-effective methods for obtaining and processing titanium alloy powder, aiming to make 3D printing with these materials more accessible for various industries.
2. Process Optimization
Achieving optimal printing parameters, such as laser power, scanning speed, and powder bed conditions, is crucial for ensuring the mechanical properties of printed titanium components. Researchers are continually refining printing processes to enhance part quality and reduce defects.
3. Material Purity and Consistency
Maintaining the purity and consistency of titanium alloy powder is critical for producing reliable and high-quality printed parts. Ongoing efforts in material science and powder metallurgy aim to improve the production processes and quality control measures to ensure uniformity in the powder feedstock.
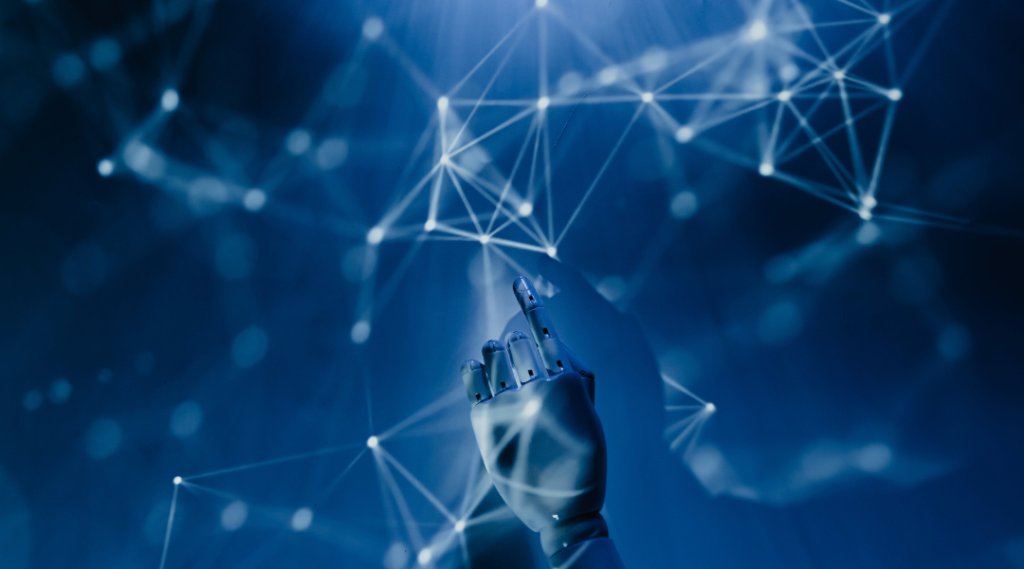
Future Outlook
1. Industry Adoption
As research advancements address current challenges, the widespread adoption of 3D printing with titanium alloy powder is anticipated. Industries such as aerospace, healthcare, and automotive are likely to integrate this technology into their manufacturing processes for lightweight, high-performance components.
2. Expanded Material Portfolio
In addition to titanium alloys, researchers are exploring the 3D printing of other advanced materials, such as titanium aluminides and nickel-based superalloys. The future may see an expanded portfolio of printable materials, further broadening the application range of metal additive manufacturing.
3. Sustainable Practices
Efforts are underway to develop sustainable practices within the titanium alloy powder production and 3D printing processes. This includes exploring recycled or eco-friendly sources of titanium and optimizing manufacturing techniques to minimize waste, aligning with the growing emphasis on environmentally conscious manufacturing.
In conclusion, the continuous advancements in 3D printing of titanium alloy powder are paving the way for a transformative future in metal additive manufacturing. Overcoming current challenges and ongoing research efforts are shaping an industry where lightweight, customizable, and corrosion-resistant components can be efficiently produced, opening new frontiers in engineering and design.