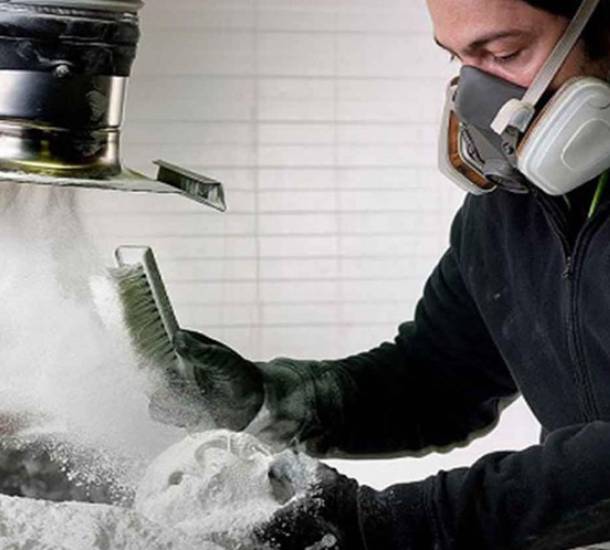
Post-Processing for 3D Printing
Post-processing of 3D printed parts is often overlooked but additive manufacturing has moved beyond prototyping to produce end-use parts directly for the consumers, the look and feel is becoming of greater importance. This is where post-processing plays an active role to achieve the required finish. Post-processing 3D printed parts helps remove excess material and a prerequisite for painting or coloring a part. Following is a list of post-processing methods applied on various parts depending on the customer’s requirements.
Clear coating:
It is a post-processing technique commonly applied to parts to obtain a cosmetic finish. As painting is also possible on 3D-printed parts, often a little polishing is needed to make the surface smooth, after which the part can be painted with whatever colors you like. You just need to get the Pantone numbers with your design upload, along with a CAD model showing which color goes where and the parts can be sprayed with an automotive-grade paint or Soft-touch painting for an attractive finish.
Plating:
Plating on 3D-printed parts is required to increase strength and durability. Electroless nickel plating can be used on a cast aluminum or magnesium part to make it look more elegant and best used for light-weight use.
Dyeing:
Parts manufactured through stereolithography (SLA), selective laser sintering (SLS), Multi Jet Fusion (MJF), and PolyJet parts can be dyed black, green, red, blue, or yellow. The finished parts are just exposed to a hot dye for a short while to achieve a prominent color. This option is one of the fastest and cost-effective ways to make printed parts look aesthetically appealing.Â
Decaling:
You can attach company logos, safety warnings, and other graphics to make a part exclusive for your company. Adhesive and thermal-transfer decals often won’t stick to the rough surface of some 3D-printed parts and sanding or smoothing is a prerequisite for decaling.
Texturing:
It improves the finish, ergonomics, and cosmetic look of 3D-printed parts by making them less slippery. This technique can apply a soft-touch paint or urethane clear coat to a 3D-printed part, to improve weather and sun resistance on the UV-curable materials used with SLA.
Polishing:
It is done over 3D-printed parts to create a high-quality finish. Some level of smoothing is often required to apply paint and decals. However, If a higher finish is a requirement then you need to specify your finish expectations and the manufacturer can do it for you.
Heat treating:
It is ideal for metal parts built with direct metal laser sintering (DMLS) to remove heat-induced stress and potential warping. It’s also used to harden, strengthen and make DMLS metals less prone to cracking and fatigue. If an extremely tough and hardened 3D-printed metal is your requirement then stainless steel 17-4 PH is the best option out there.
There are many post-processing options available and depending on the material type and requirement, the best technique is selected and applied on the 3D printed part to achieve the desired finish.
Our Clients
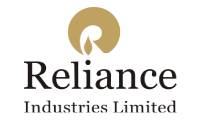
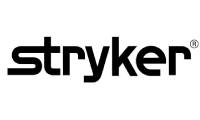
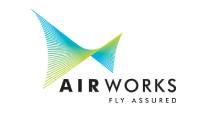
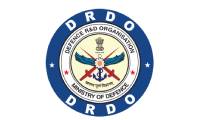
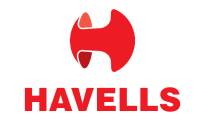
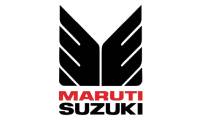
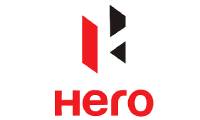
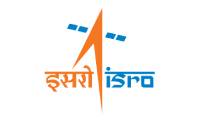
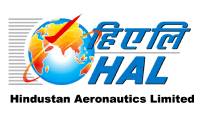
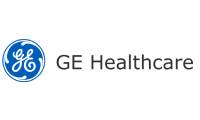
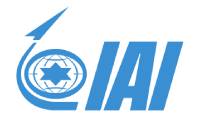

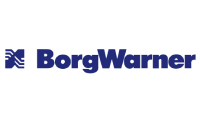
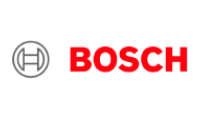
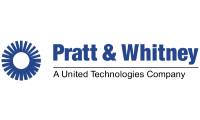
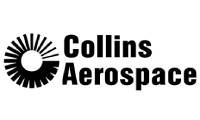
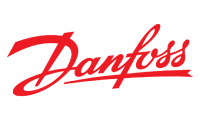

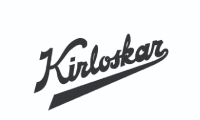

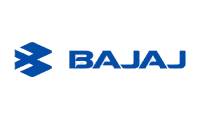
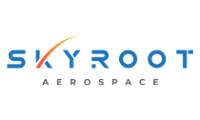
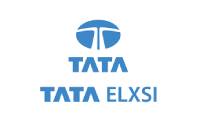
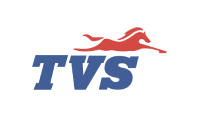
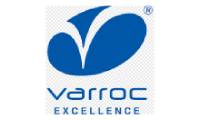
1 Million +
Parts Built
25+ Parts
Built Every Hour
ISRO, DRDO, MRO
Collaborations