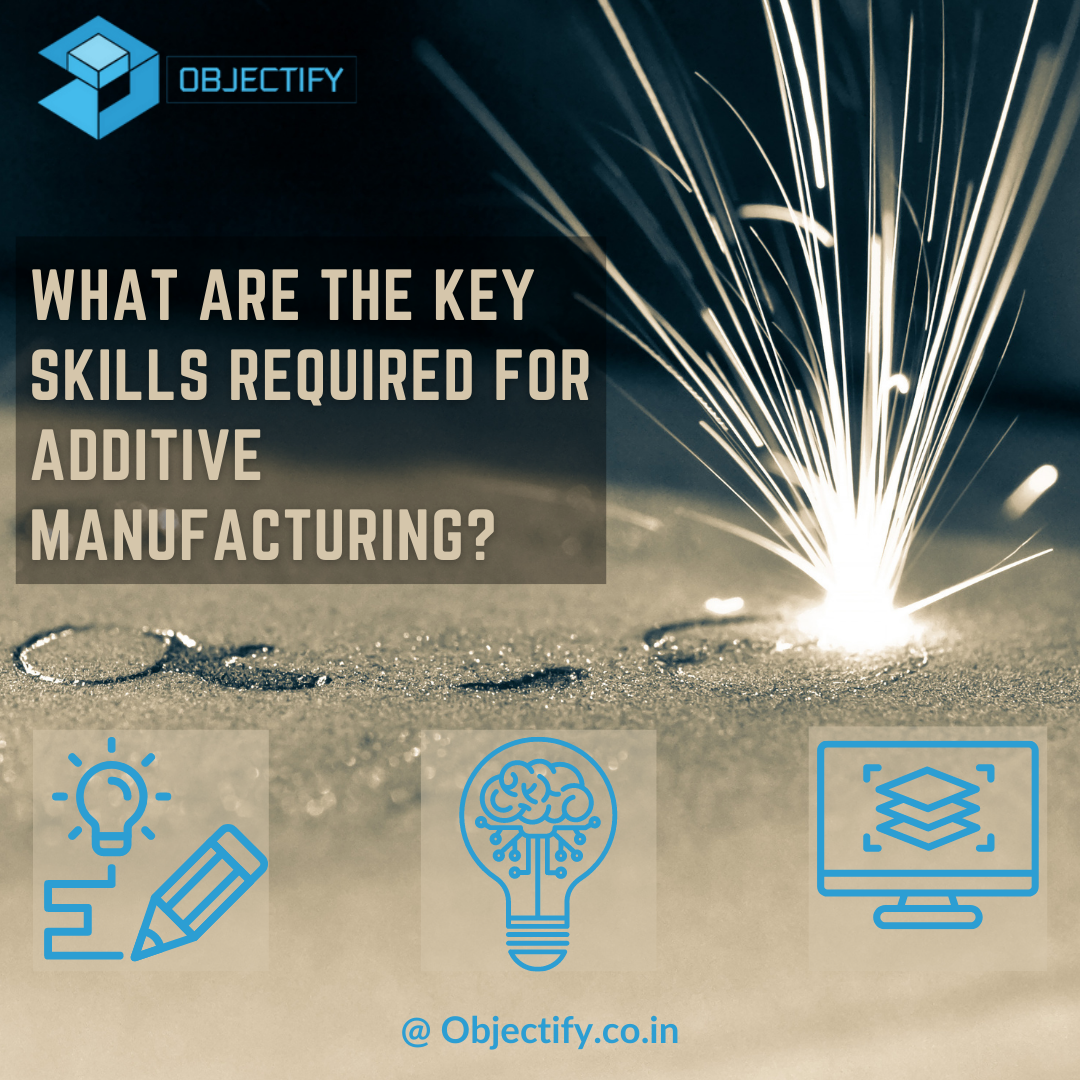
SKILLS REQUIRED FOR ADDITIVE MANUFACTURING
Additive Manufacturing or 3D Printing is the process of making solid objects from a digital file by laying down successive layers of material; which is very different from traditional manufacturing processes which removes or subtracts material to form the desired shape. The transition or switch from one form – traditional to additive can be challenging in various ways. Thus, there is a skill gap in the workers; without the right set of skills, it is difficult to train workers at a fast pace.
Some essential skills required for Additive Manufacturing:

Design knowledge of CAD
1. Understanding of the concept of design knowledge of CAD
In additive manufacturing, the designer is set free from the manufacturing constraints of the traditional methods and has the freedom to design a component in a way which has maximum weight reduction and minimum material consumption while meeting the client’s need. Complex geometries and structures like voids, lattices and other hard to manufacture structures can be used to cut down weight and material consumption.
As 3D data is used to create or produce the geometric form of the component. The knowledge and creativity of a CAD designer is required in AM. Designing, modifying or improving an existing 3D model is very critical in AM. The 2D data given by the companies need to be remodelled into a 3D data. The geometric and design considerations should be taken into account while remodelling. The part needs to be remodelled in a way in which the least amount of material is needed, eliminating all the unnecessary features from the part to reduce its weight.

2. Design for Additive Manufacturing (DfAM)
DfAM is the art, science and skill of designing for 3D printability
The layer based additive nature of AM allows designers a lot of space for customization and to print complex geometries. With the help of tools (generative design, topology optimization, lattice structures), lighter, stronger and more efficient designs can be created which would require less material consumption. Various features can be introduced in the complex part without the simplification which is required in most conventional processes.
The approach needed for Additive Manufacturing is very different from that of the conventional manufacturing methods. As in AM, manufacturing is done by adding layer by layer instead of removing material from a block of material. Engineers will start ‘thinking additively’, opening up a lot of space for creativity and design freedom. The knowledge of design for orientation, contour design, adding hardware, and minimizing complications is very important for creating a 3D printable file to feed the 3D Printing machine.
3. Eye for Opportunity
Remain vigilant on keeping an eye open for trends, issues and opportunities where the business can leverage for success.
It is the skill to lookout for an opportunity where AM can be applied and utilised to its maximum potential. Innovation and ideation will play a major role in developing an eye for opportunity.
4. Creation of Business Case
A Business case is created to evaluate the benefits, cost and profits of a project while taking risk factors into consideration and provides a rationale for a preferred solution. It is usually developed during the early stages of a project.
Factors that are taken into consideration while creating a business case are: Reasons, options, benefits, costs, timescales, and risks.
5. Material selection
The material that can be used for AM can be determined according to the type of machine and the requirement of the part. 3D printing materials are thoroughly tested in order to find the various properties and characteristics in different environments. Select the material by its mechanical properties- Yield strength, tensile strength, elongation, hardness, etc. that corresponds with the primary function of the part.
6. Understanding of manufacturing technology
There are various types of additive manufacturing having different methods:
· VAT Photopolymerisation
· Material Jetting
· Binder Jetting
· Material Extrusion
· Powder Bed Fusion
· Sheet Lamination
· Directed Energy Deposition
Electron Beam Melting (EBM), Direct Metal Laser Sintering (DMLS), Selective Heat Sintering (SHS), and Selective Laser Melting (SLM) are slight variations of Powder Bed Fusion.
Selection can be made on the basis of functionality of the product:
Based on part’s form/fit – tolerance of the part; FDM is the lowest tolerance method (+0.5mm) and Material Jetting SLA/DLP for producing parts with high tolerance (+0.1mm or less)
Based on part’s strength- FDM produces parts with strength (<30 MPa), SLS with strength 30-85 MPa; obtain the highest strength (>85 MPa) using DMLS/SLM;
Based on part’s flexibility – either high elongation (FDM, SLS) or soft/rubber-like; based on special properties like chemical resistance, heat/flame resistance, biocompatible, etc.
On the basis of visual appearance: smooth surface, transparent, texture, color, etc.
Selecting an appropriate method which will be most suitable for a part made of a particular material is important as that would determine the built quality, time and accuracy of the produced part.

7. Finishing
Finishing is essential in 3D printing as layered 3D printed production parts may not be that accurate to the final dimensions or may not have a great surface finish. So in order to avoid the appearance of the layer effect on 3D printed parts Post processing is required after printing the parts in the 3D printer. Supports from the build need to be removed, processes like grinding, sanding, cutting, filing, painting, coating, polishing are also applied as per the requirements.

Quality – Most 3D printed metal parts are heat treated. Treatments remove the internal stresses formed during the printing process and the microstructure of the part can also be changed as required. By heat treatment material can be made stronger, tougher, more durable, and more resistant to wear.
8. Safety
Proper handling of materials, understanding of material properties and operating safety equipment is necessary in Additive Manufacturing. In metal additive space, materials management and environmental waste disposal knowledge is a major concern and is not a thing to be overlooked upon. There is also specific training for Personal Protective Equipment (PPE), Fire Safety and proper waste management procedures.
The materials (resins) used are in the form of solids or liquids; when these are used in Additive Manufacturing processes emit hazardous fumes, volatile organic compounds and other emissions when processed.
Metal powders used in AM processes are very small in size, mostly microscopic (<100 µm). These powders are toxic, reactive, combustible, and unstable posing various hazards to those who work in such an environment. Other health risks are caused from inhalation, ingestion or contact with the skin
CONCLUSION
The Additive Manufacturing process chain includes – Procurement, Product Development, Manufacturing planning and Production. Product development includes design for AM and its validation; manufacturing planning includes build preparation and simulation; Production includes machine connectivity, scheduling & execution, post processing and Quality & Analytics. With an in-depth knowledge in the AM process chain, one will be able to successfully produce parts using Additive Manufacturing technology