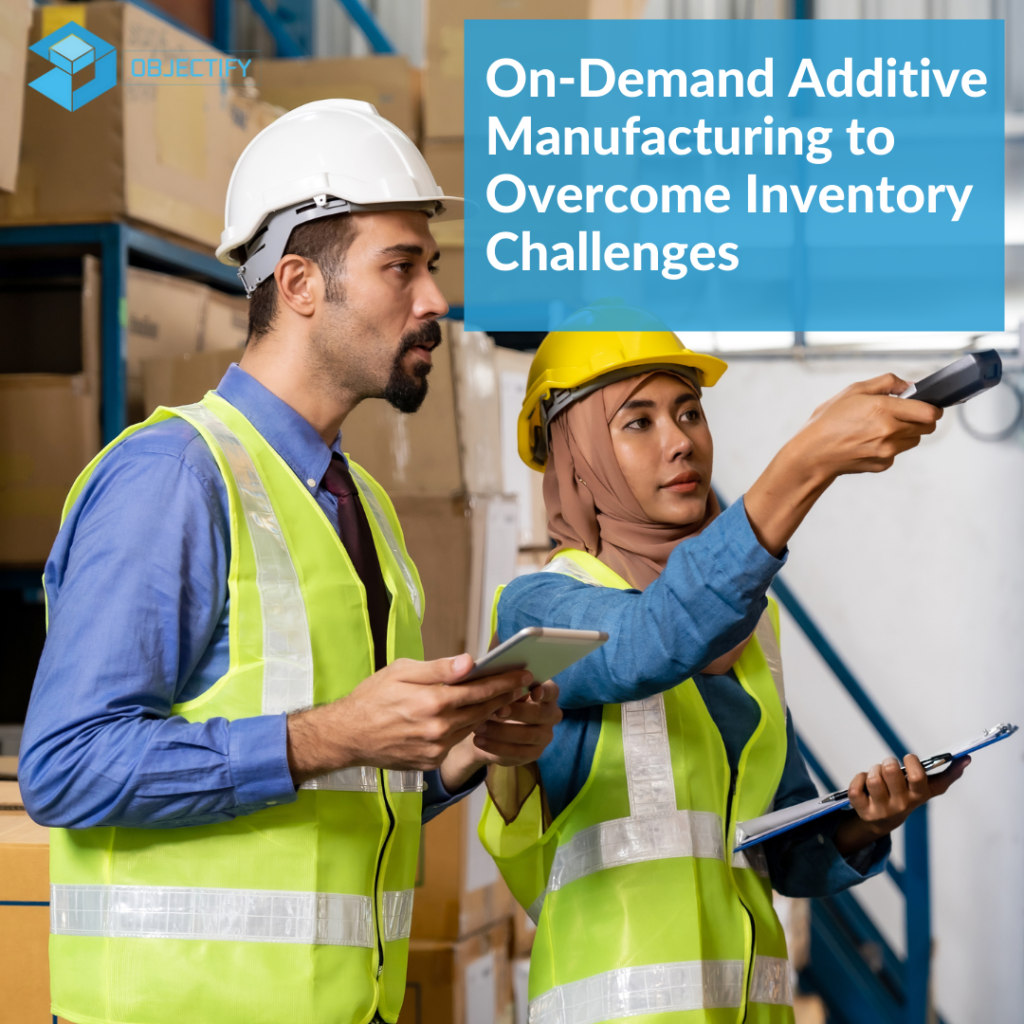
On-Demand Additive Manufacturing to Overcome Inventory Challenges?
The fact that Original Equipment Manufacturers(OEMs) go through many challenges related to supply chain management is no more a secret today. High investment to house spare and replacement parts, maintaining a safe physical inventory, and cost of inventory management programs, etc. are some of the prominent challenges to name.
These inherent complexities of varying degrees created a wide felt necessity among the OEMs to supplement the conventional methods of production with emerging technologies like additive manufacturing (AM), or 3D printing.
AM is a computer-controlled production method that creates three-dimensional parts by depositing the material layer by layer to produce the parts and meets any on-demand volume with a much lower latency. However, this method is best suitable to produce small-batches of parts.
Challenges of Warehousing Automotive Parts:
The automotive industry is a perfect example as it needs a host of vehicle parts that are produced in higher volumes and need to be stored at multiple locations to meet consumer demands and quickly serve the requirements. They follow the same conventional manufacturing and storing the product components on warehouse shelves that may get occupied for any uncertain period of time as there is no proven method to project and predict the requirement of the spare parts. Sometimes the OEMs start feeling it as a dead inventory and find small distributors to sell the soon-to-be-obsolete parts with a much lower price which causes a financial loss to the part manufacturing companies.
This is an instance where additive manufacturing can truly flourish as a method to create parts and meet the demands of consumers. Preparing to transform your production method is important to apply AM as a tool to manage product storage needs. When considering a partnership, take enough care to choose an AM supplier that has on-premises manufacturing facility, certified process and qualified engineers. Forget not to inquire, if these manufacturing specialists are focused on the automotive part production process. A highly organized approach will definitely help OEMs get quality parts now and every time they have an on-demand order.
Overstocking parts not only increases the investment but also a large warehouse space, and maintaining physical inventory is very much challenging and costly. Here are the advantages of Additive manufacturing or metal 3d printing to overcome supply chain and inventory management problems.
Five Advantages Of Additive Manufacturing
1. Production Decentralization:
AM is a quiet portable technology that helps companies to be able to get production to local markets quickly. Companies find better solutions to manufacture components locally instead of relying on imports. It reduces the cost of the product and a contentious supply of parts remains unaffected during any geopolitical uncertainties like the current war situation.
2. Easy product customization:
Since 3D printing is independent of any physical molds, manufacturers get enough flexibility to customize the parts and easily meet the unique needs and improve the consumer experience. With one AM partner, designing, manufacturing, and delivery can be merged into a single supply chain function, reducing the manufacturing and inventory management cost.
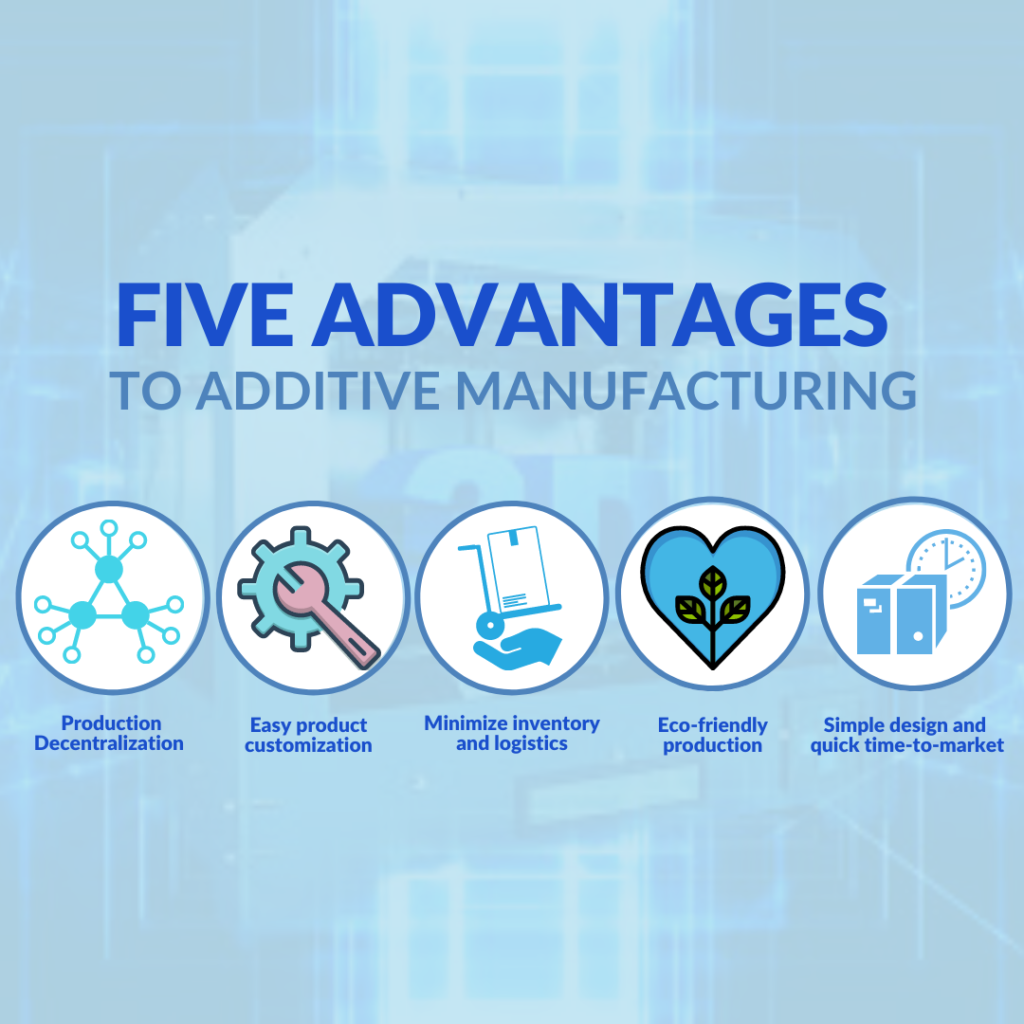
3. Simple design and quick time-to-market:
3D printing technology can produce a part with minimum joints making the manufacturing process easy and increasing the part durability. Simplified designs improve lead times, and shorten time-to-market thereby affecting the supply chain.
4. Eco-friendly production:
3D printing is an environment-friendly and cost-effective manufacturing process. It produces almost no waste with a lower carbon footprint. You can better regulate overproduction and surplus inventory with its ‘Just-in-Time’ manufacturing capability.
5. Minimize inventory and logistics:
With ‘on demand’ manufacturing, the need to move physical products across geographies will reduce and this will certainly have a significant effect on warehousing and logistics, benefiting the customers to get the finished part at a lower price.
AM is a comparatively new technology and every day new improvements are pushing 3d printing to new heights. However, currently, there are limitations to AM being the ultimate solution for OEM challenges. Here are some examples:
• OEMs need many small parts and often moving parts that streamline repair and replacement processes and sometimes it is difficult to produce these parts with AM.
• AM may not be employed to produce some of the highly aesthetic components.
• The selection of raw material for AM is limited and it must be verified and validated to meet industry and regulatory standards before being used in real production.
Conclusion:
Both manufacturing processes and consumer demands continue to evolve and to better manage this situation, OEMs put all their efforts to apply AM in the production process as much as possible to push on-demand production to the next level. However, there will always be a need for physical inventory, but 3D printing reduces its need and management cost.
To apply AM into your operations strategy effectively, you need to have a discussion with your manufacturer to formulate a strategy with measurable goals as AM can’t be realized overnight. Partner with Objectify Technologies Pvt Ltd, one of the pioneers in the field of additive manufacturing, and rapid prototyping in India since 2013 to serve all your needs from fully functional prototypes to production parts.