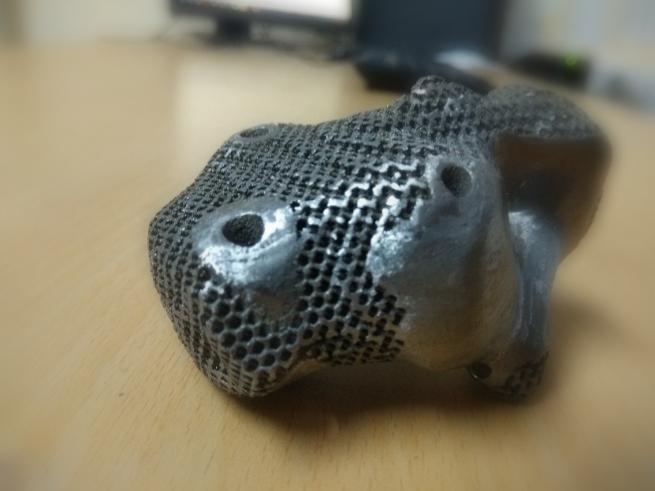
The Problem
Doctors from Maulana Azad Medical College (New Delhi) had an immediate requirement of a heel bone implant for a patient suffering from bone cancer.
The requirement needed to be met as soon as possible as the cancer was spreading, effecting more bone tissues. Current Bone Grafting techniques are inadequate to meet the demand of cancer-ridden cells. This would have led to Amputation.
The Challenge
The Challenge was to Avoid the need for Amputation.
The Heel Bone Implant needed to have had the desired surfaces for ease in joining along with pores for Osseointegration and lightweight for mobility. The implant also needed to last longer without causing any discomfort hence it needs to have customized the shape for perfect replacement, accuracy for ease in movement and strength for durability.
The Solution
With the help of the CAD file of the ankle obtained through CT scan, OBJECTIFY started working on providing a solution. Metal Additive manufacturing was the only tool that could address the requirements and that too in such a short timeframe. Using Polymer-based 3D printing technology (SLS – Selective laser Sintering) the team created a mock-up for the final end implant.
Selective Laser Sintering (SLS) 3D Printing is an additive manufacturing technology that uses a powerful laser to sinter polymer or metal powders layer by layer to build a solid part by scanning the cross-section of a 3D digital design. We manufacture high-quality 3D parts by using some of the top-of-the-line rated printers in the industry such as EOS P 396 and EOS P 110.
Build Volume of P 396 – 340 x 340 x 600 mm
What makes SLS an excellent choice for producing production parts?
SLS is an additive manufacturing technology that uses powdered Nylon 11 , Nylon 12 and PEEK materials
Parts produced are light-weight, highly durable, High throughput and both heat and chemical resistant, making SLS an excellent choice for producing production parts without the expense of tooling.