Additive Technology
Metal Additive Technology
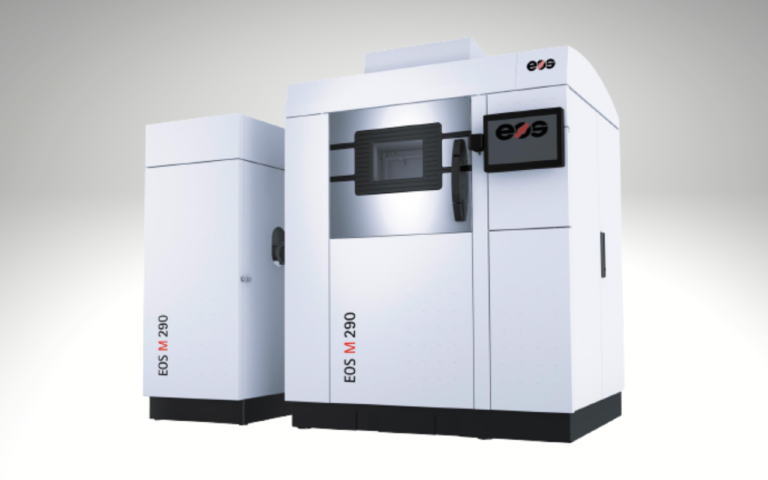
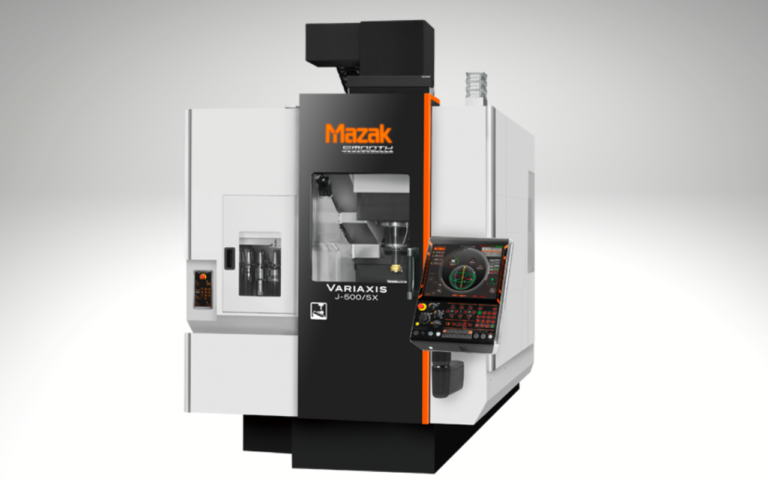
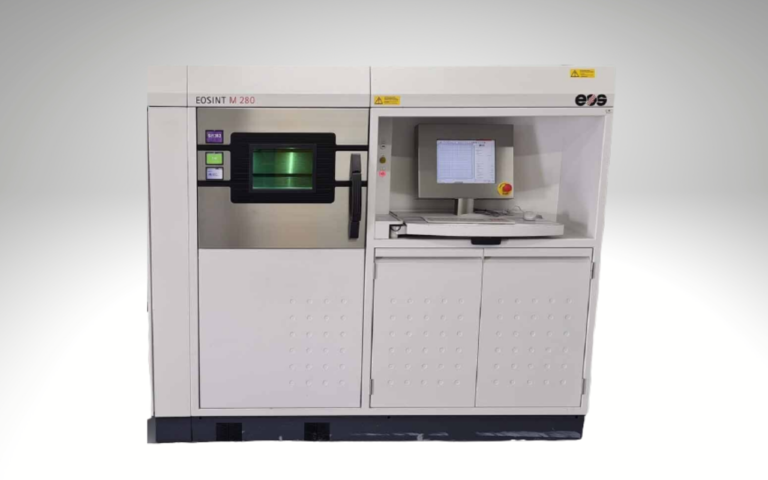
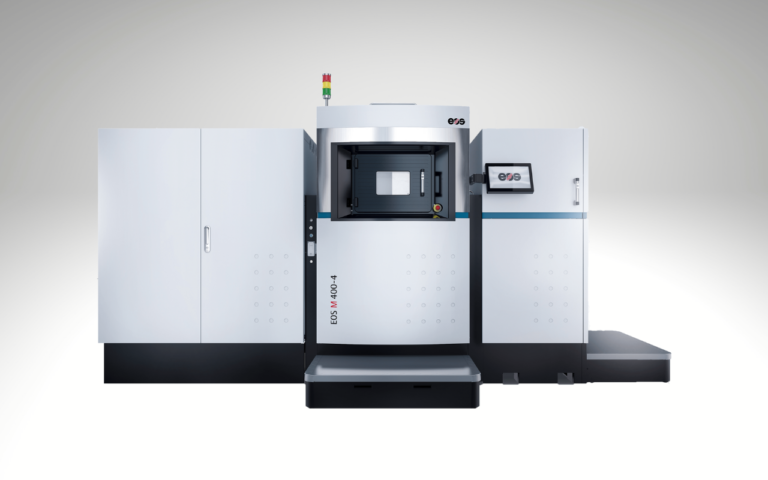
Direct Metal Laser
Sintering (DMLS)
DMLS process enables the fabrication of fully dense 3D Structures by selective melting of micro-sized metal powder using a high-intensity laser beam. Due to its ability to form fully dense structures, the mechanical properties are equivalent to those achieved by the use of conventional manufacturing methodology.
Computer Numerical
Control (CNC)
Conformal
Cooling
Polymer Additive Technology
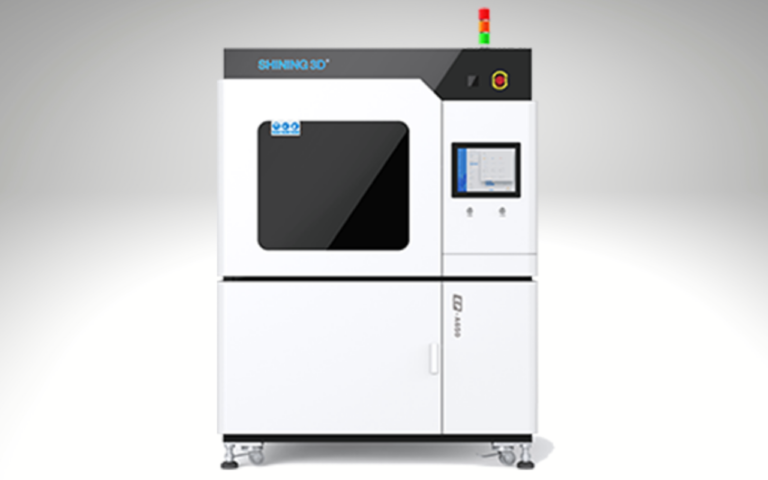
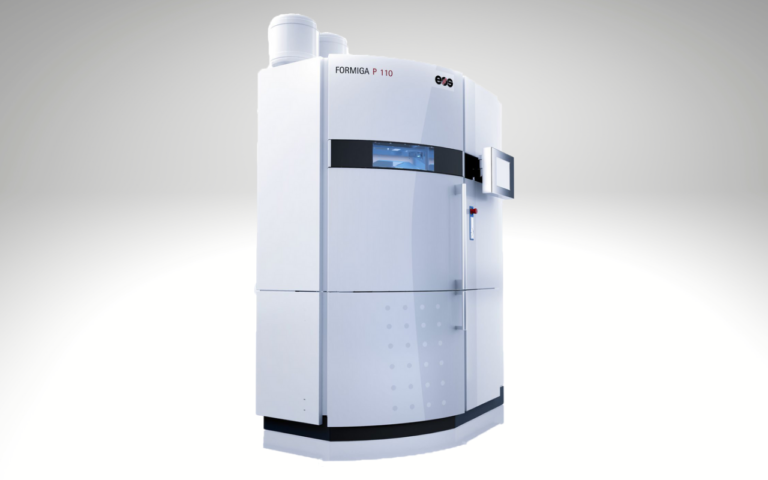
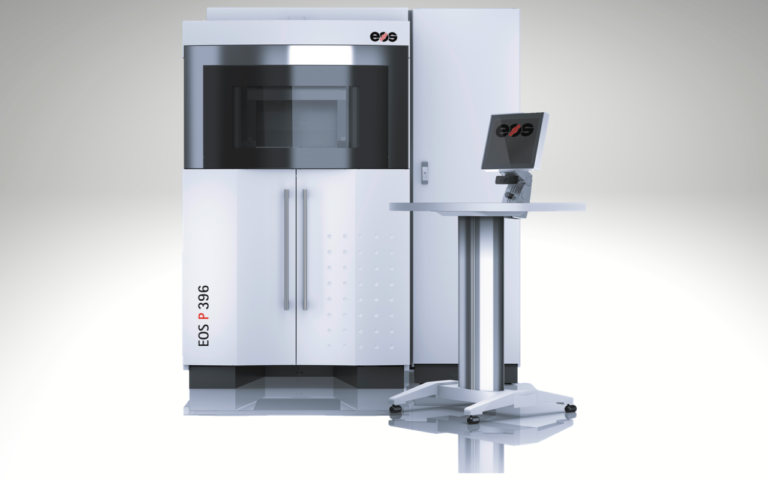
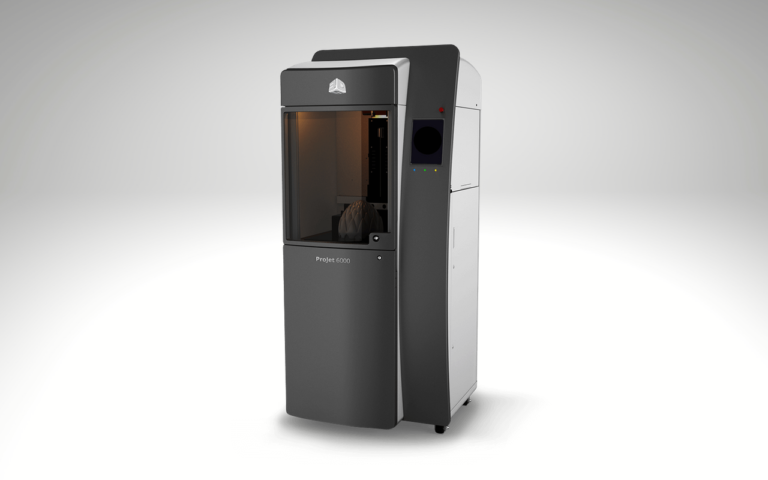
Selective Laser Sintering (SLS)
Laser Sintering (LS)—often called Selective Laser Sintering or SLS is an additive manufacturing process that enables the fabrication of polymer based 3D structures directly from digital data.
During the process, micro-sized polymer powder is selectively sintered to form a 3D Structure in a layer by layer methodology. Thus, eliminating the need for any dye or remnant material. LS parts have exceptional strength, accurate dimensions, light weight and heat resistant properties.
Stereolithography (SLA)
It is a form of 3-D printing technology used for creating models, prototypes, patterns, and production parts in a layer by layer fashion using photo polymerization.
Vacuum Casting
Patterns are 3D solids of your CAD designs. They are usually made by CNC machining or with 3D plastic printing such as Sla/SLS. You can supply your own patterns or we can make them for you. Patterns need to be able to withstand heating to 40°C.
Casting moulds are made from liquid silicone. This silicone is poured around the master pattern inside of a casting box, and then allowed to cure in an oven for 16 hours. Once dried, the mold is cut open and the master removed, leaving behind an empty cavity in the exact negative shape of the original.
Your choice of casting resins can now be poured into the empty cavity to create a highly accurate copy of the original. It’s even possible to overmold with two or more materials. Silicone molds are typically good for 20 or so copies of the master pattern.
