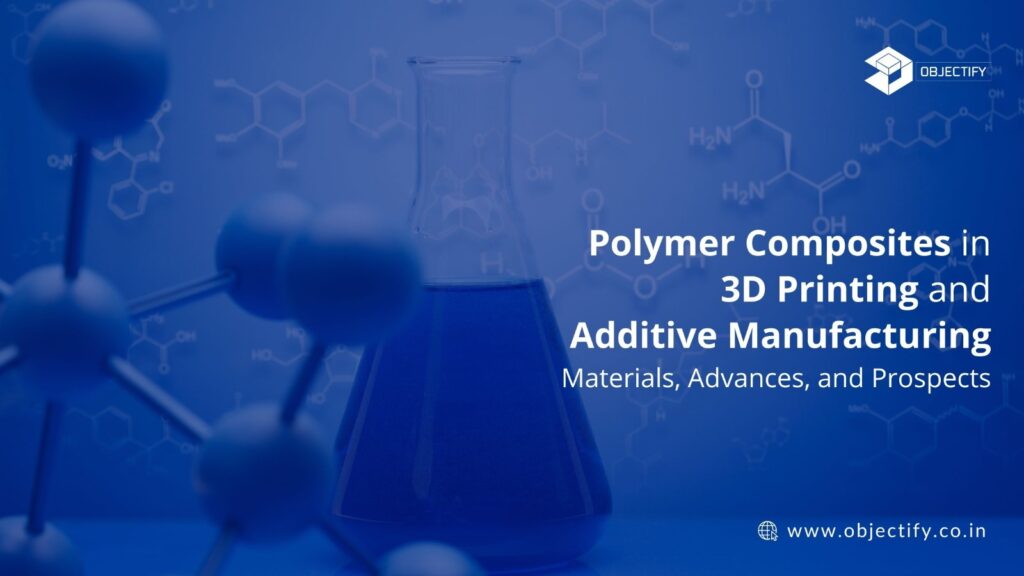
Polymer composites play a significant role in the realm of 3D printing and additive manufacturing, offering diverse materials, advanced techniques, and promising prospects. Let’s delve into these aspects:
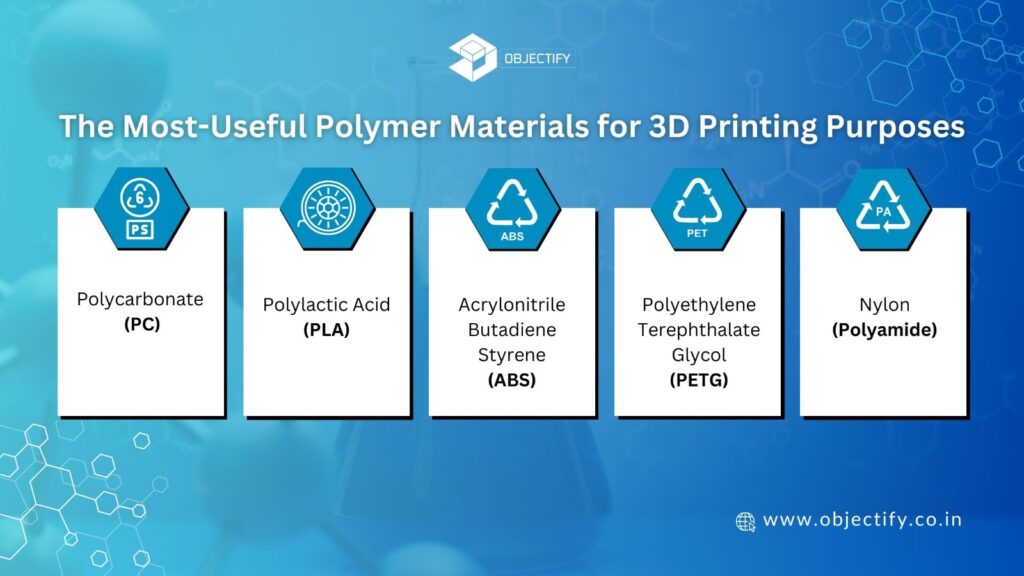
Materials Diversity:
Polymer composites encompass a wide range of materials, including thermoplastics, thermosets, elastomers, and reinforced polymers. These materials can be combined with additives such as fibers, nanoparticles, and fillers to enhance mechanical, thermal, and electrical properties. Carbon fiber, glass fiber, Kevlar, and graphene are commonly used reinforcements in polymer composites for 3D printing.
Advanced Techniques:
Additive manufacturing techniques, such as Fused Deposition Modeling (FDM), Stereolithography (SLA), Selective Laser Sintering (SLS), and Multi Jet Fusion (MJF), enable the fabrication of intricate structures with polymer composites. These techniques allow for precise control over material deposition and layer-by-layer construction, resulting in complex geometries and tailored material properties.
Enhanced Performance:
Polymer composites offer superior mechanical properties compared to pure polymers, making them suitable for applications requiring strength, stiffness, and durability. By optimizing the composition and fabrication parameters, researchers can tailor the properties of composite materials to meet specific performance requirements, such as high strength-to-weight ratio, thermal stability, and chemical resistance.
Functional Integration:
Additive manufacturing facilitates the integration of functionalities within polymer composites, such as embedded sensors, actuators, and conductive traces. This enables the production of multifunctional components and devices with added sensing, actuation, or connectivity capabilities, expanding the application scope of polymer composites in fields like aerospace, automotive, healthcare, and electronics.
Design Freedom:
3D printing offers unprecedented design freedom, allowing engineers to create complex shapes and structures that are difficult or impossible to achieve using traditional manufacturing methods. Polymer composites further enhance this design flexibility by offering a wide range of material options and the ability to incorporate gradient structures, lattice geometries, and topology optimization techniques for lightweight and efficient designs.
Sustainability:
Polymer composites in additive manufacturing can contribute to sustainability efforts by enabling the use of recycled or bio-based polymers, reducing material waste, and optimizing energy consumption. Furthermore, lightweight composite structures can lead to fuel savings in transportation applications, while the ability to manufacture on-demand and locally can minimize supply chain logistics and carbon footprint.
Challenges and Future Directions:
Despite the numerous advantages, challenges such as material compatibility, process scalability, surface finish, and post-processing requirements remain to be addressed. Future research efforts are focused on developing novel composite formulations, optimizing manufacturing processes, advancing in-situ monitoring and quality control techniques, and exploring new applications in areas such as tissue engineering, energy storage, and wearable devices.
In conclusion, polymer composites have emerged as versatile materials in 3D printing and additive manufacturing, offering a wide range of materials, advanced techniques, and promising prospects for enhanced performance, functional integration, design freedom, sustainability, and innovation across various industries.