As the name suggests, 3D printing or “Additive Manufacturing” is a keen process of manufacturing three-dimensional objects from a digital file.
The making of a 3D printed object is made possible using an “Additive” process. In an additive process, an object is created by laying successive layers of material one after another until the object is formed completely. Each of the coatings can be seen as a thinly sliced horizontal cross-section part of the last object.
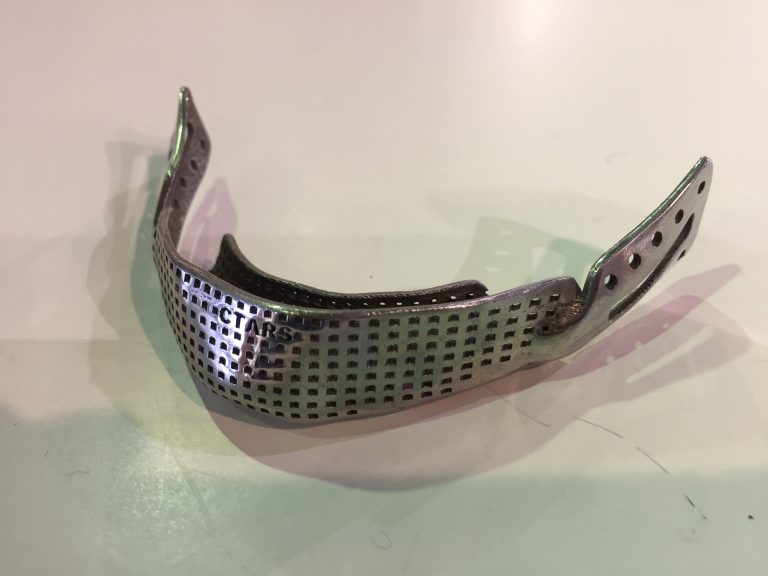
3D printing is the opposite of “Subtractive Manufacturing,” which is nothing but cutting or hollowing a piece of metal or any plastic, with the help of a suitable milling machine.
3D printing enables you to produce very complex shapes using very little material as compared to traditional manufacturing methods.
3D printing technology has been successfully implemented in various domains such as aviation, automotive, construction, medical, etc. Out of this, we are going to explore applications of the 3D printing process in the medical domain in detail.
The flexibility and durability of the 3D printing process allow designers to make quick and crucial changes in a hassle-free way without the need to set up any kind of additional equipment or tools. It also enables 3D manufacturers to create equipment matched to a patient’s anatomy (patient’s need specific devices) or equipment with very complex internal structures that are hard to design manually. These capabilities have sparked massive interest in 3D printing of medical devices and other products, including food, household items, and automotive parts, as well.
Medical equipment and implants produced by 3D printing include orthopedic and cranial implants, surgical equipment, dental restorations such as crowns, and external prosthetics.
Due to its versatility, the 3D printing process has vast medical applications in the below fields:
- Medical devices regulated by FDA’s Center for Devices and Radiological Health (CDRH),
- Biologics regulated by FDA’s Center for Biologics Evaluation and Research, and
- Drugs regulated by FDA’s Center for Drug Evaluation and Research
Medical equipment and implants manufacturers should always refer to FDA guidance documents and Quality Systems regulations for more information on specific applications in the medical field.
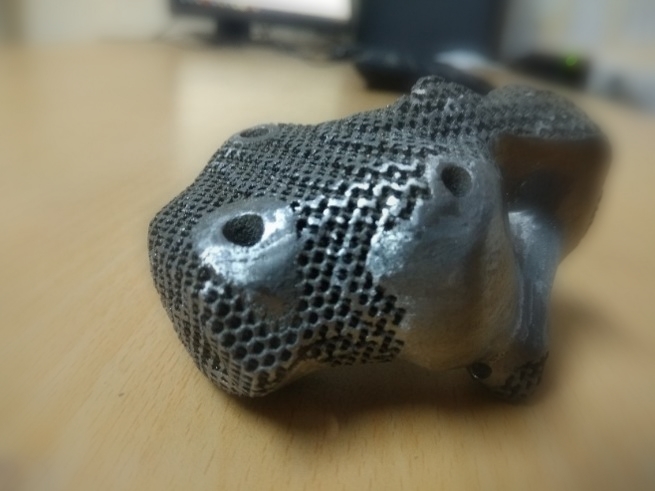
As we saw, the 3D printing process is used to manufacture a variety of durable and versatile medical devices, which also include those with complex geometry or tedious features and functions that match a patient’s unique anatomy (needs to live the life comfortably
There are two ways of3D printing designing in the medical domain. Some types of equipment are printed from a standard, popular design to make multiple and identical copies of the same device. Other devices, which are also called patient-matched or patient-specific equipment, are created from a specific patient’s imaging data that will meet the patient’s particular requirements.
Commercially and quickly available 3D printed medical devices generally include:
- Instrumentation (e.g., guides to assist with the proper surgical placement of any equipment)
- Implants (such as cranial plates or hip joints)
- External prosthesis (e.g., hands)
Scientists are performing R&D on how to successfully use the 3D printing process to manufacture living human organs such as a heart or liver, but this research is in the primary stages of development right now.
The 3D printing process can be implemented nowadays using any of several different cutting-edge and top-notch technologies. The suitable choice of technique can depend on many factors, including how the final product will be used, in which domain it will be used, and how easily the 3D printer can be used. The most common technique used for 3D printing medical equipment is called “Powder Bed Fusion.” Powder bed fusion is generally used because it works with a variety of manufacturing materials used in medical equipment, such as Titanium and Nylon.
The powder bed fusion process builds a 3D product from excellent metal or plastic powder. This powder is poured onto a platform and leveled carefully first. A laser or electron beam is then moved across the powder layer and starts melting the material it touches. The melted plastic is then fused to the layer below it and to the powder around it to create a solid substance. Once a layer is completed, the platform is moved down, and one more layer of carefully leveled powder is placed on top of it.
The FDA owns several 3D printers that help us better recognize the capabilities of 3D printing of medical equipment and the public health benefit of this technique. For example, the FDA has printers that use different printing techniques, including powder bed fusion, to evaluate what parts of the 3D printing processes and workflows are critical to ensure the quality of the finished medical equipment.
Now, let us see a case study that shows how Objectify Technologies from Delhi created DMLS Titanium Calcaneus Implant for a patient who was suffering from bone cancer.
Doctors from Maulana Azad Medical College (New Delhi) had an immediate requirement of a heel bone implant. The condition was needed to be met soon, and the patient’s relatives and the patient himself wanted to avoid the amputation at any cost. The timeline was crunched to one week. Objectify Technologies made it happen within a timeframe in the following way:
With the help of the CAD file of the ankle obtained through a CT scan of the patient, Objectify Technologies started working on the customized 3D model of the bone implant. Metal additive manufacturing was used to meet the requirement successfully.
Using Polymer-based 3D printing technology (SLS – Selective Laser Sintering), the team of Objectify Technologies created an effective mock-up implant for the testing. It was tested successfully, and then the end implant was manufactured and given to doctors for using the same.
Talking about the future of 3D printing technology in the medical domain, we must say that this is evergreen and never-ending technology. This technology will be continuously evolving, and providing relieves to patients suffering from dangerous diseases. Firms such as Objectify Technologies are marking their footprints in this field to become a pioneer and guide others to revolutionalize this technology.